project H:Pitch
Indicates Dynamic way of expanding from flat surface into fabricated system
Process
Users would treat this not only as constructed object but also as an integral enhancement of the site. Our concept "Symbiosis" in a way reflects this very phenomenon.
SPATIAL SPILLAGE
The surfology and its spatial types within the park topography afford the triggerings of activities within the programs of the park. These activities are of the temporal meaning that other activities can than be triggerd!
MULTI-COMPONENT SYSTEM RESEARCH
How to create a non-standard structure out of standard components?
MODULAR PATTERNS
After a long phase of research and exploration we came across a component in that we are able to achieve a variety of form and space from single basic geometrical shape (i.e. a triangle). Modular patterns can be deployed to form different volumes while remaining as a surface when retracted.
GEOMETRIC ANALYSIS
Nine different component geometries obtained by the combination of 3 stages in the actuators: open, semi-open and closed.
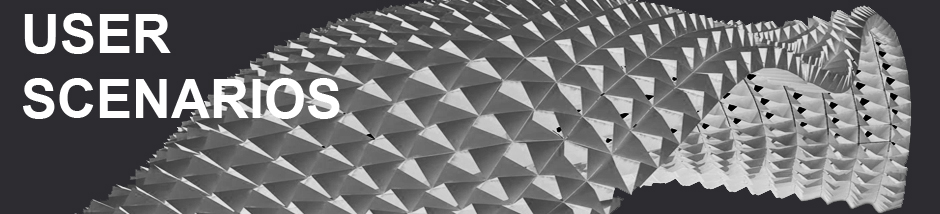
SEASONAL SCENARIOS
MEDITATION AREA
Existing trees been used as anchor points for the terrace structure, facilitating ambience for meditation space
DESIGN CHALLENGE
The component as such depends on the main structural performative system (origami), it is required for this unit to be adjustable and adaptable to its primary system. Therefore, several properties need to be adjusted such as; the overall geometry, movement range and mechanical complexity.
FABRICATION AND ASSEMBLY
In the assembly process of making 1:1 prototype, parts can be pre-assembled to step 5 for flat packaging using hinges in between. Parts from step 5 and step 6 are the only parts that need to be taken to the site for final assembly. With the 1:1 scale model, this arrangement create difficult to reach spaces and angles for the final assembly especially on verge of reaching step 7 where bike tire connections were required to be bolted. Constructing it on a desk/ studio is a challenge; however, constructing the final assembly on a real site is a different process that needs to be studied with further research.
As estimated the cost incurred for the overall manufacturing went to around 70 Euros, i.e. each component costs around 9 Euros. That was an economical and successful approach towards the prototype design considering the material and fixture costs.
We would like to end this project by summarizing and concluding our learning for further research development.